Guill Tool & Engineering’s one-bolt extrusion crosshead
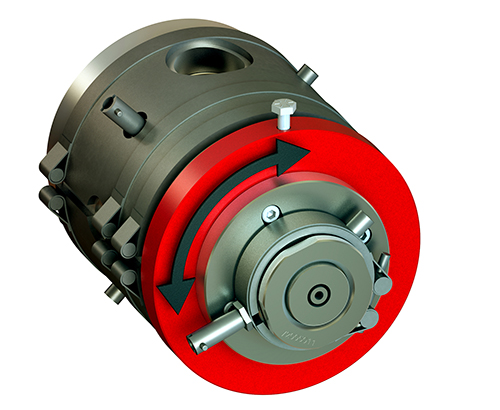
Standard crosshead designs with four adjustment bolts located 90° apart require operators to loosen one bolt and tighten the opposing bolt in order to yield a tube with a uniform wall thickness. Adjusting out any unacceptable eccentricity requires obtaining a measurement of the product’s current concentricity, which is either done as an inline process or after the extrudate has been fully cooled and cut for sampling.
“The whole time you’re making these adjustments, you’re wasting time and plastic,” said Guill product development engineer Denis Finn Jr.
The new Micro Medical crosshead has just one bolt that controls 360° of concentricity adjustment. Having just one bolt that can orbit freely around the outside of the die should reduce the time it takes to get the line running and producing quality product versus standard concentricity adjustment, Finn said.
Concentricity adjustment precision with the Micro Medical reaches 0.008 in. or finer per revolution, according to Guill (West Warwick, R.I.). The single-point crosshead includes a patented cam-lock deflector for quick changeovers. The deflector has a residence time of 1 min. at 0.5 lb/hr material flow. It has optimized usage with extruders measuring 0.5 in. and 0.75 in., and a max die ID of 0.25 in.
“In essence, it’s a total overhaul of an offering that’s existed for awhile,” he added. “Every single facet of it has been carefully revised to keep operators’ efficiency as high as possible. We’re maximizing the efficiency of the die assembly.”
The Micro Medical crosshead also accepts both vacuum and micro-air accessories and works well in pressure and sleeving applications, according to the company. Fluoropolymer designs are available upon request.